Here is the specific plan for creating a bronze award:
- 1. Sketches of original ideas on a paper for a future design.
- 2. Customer approves final drawing.
- 3. Model in clay, approval by client.
- 4. Make the first mold.
- 5. Pour plaster or wax into first mold.
- 6. Correction of all the details.
- 7. Production of final mold for the final award design.
- 8. Pour wax into the mold.
- 9. Foundry produces all the steps to finish the award in bronze: cleaning, chasing, polishing, and finishing with hot patination. Bolting to pedestal.
Everything is hand-crafted. It takes time, experience, and special knowledge to complete. Bronze lives for thousands of years.
The process of making awards in other materials is similar.
The winner deserves great quality!
Each piece is uniquely developed to meet your individual needs. We would be happy to create awards for your special event to honor the best.
Victory Bronze Making Process
1. The Original Model
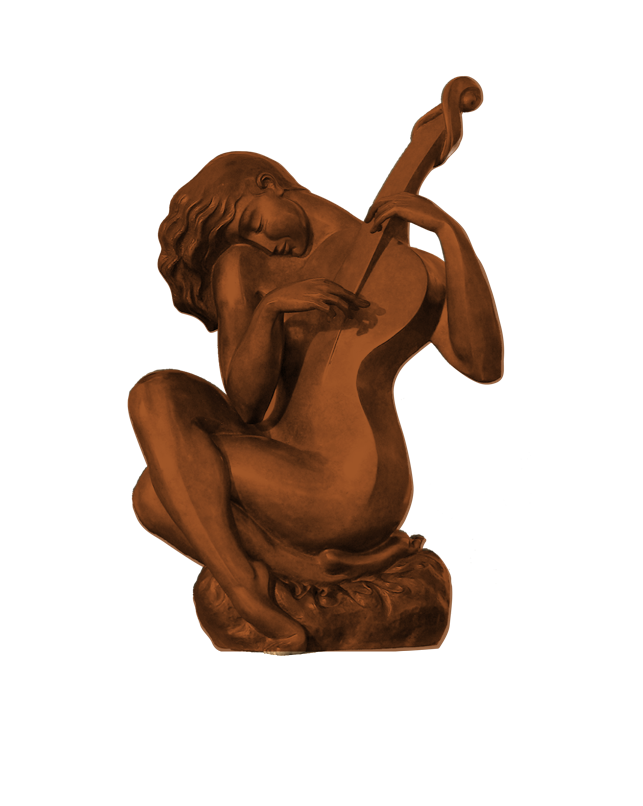
2. The Rubber Mold
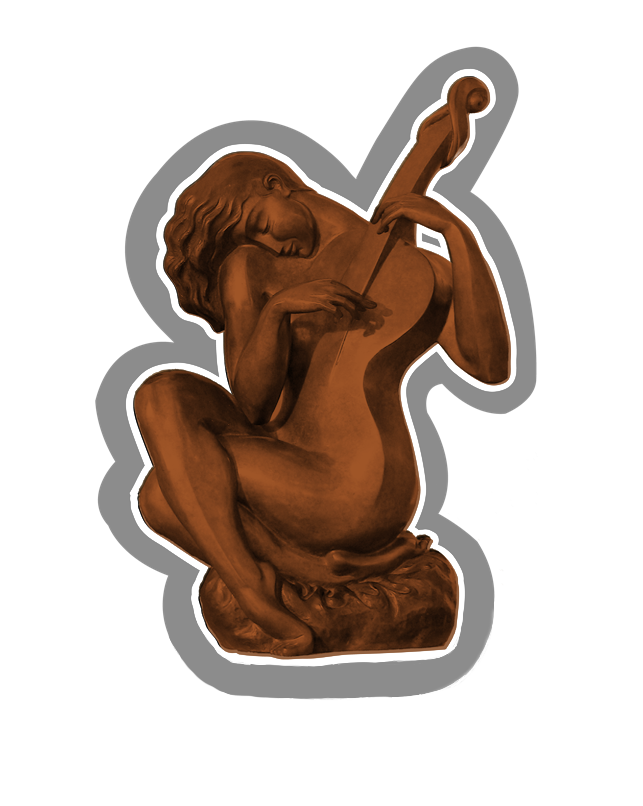
3. The Wax Duplicate
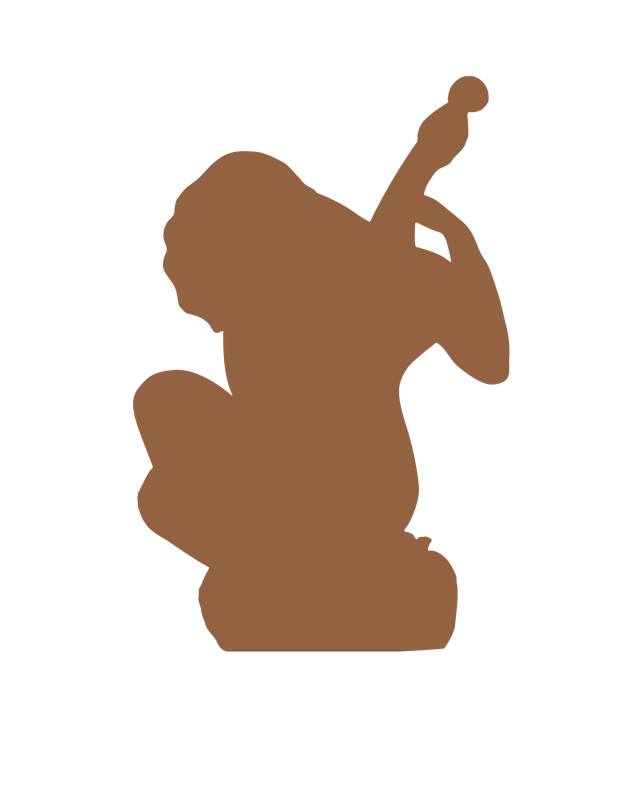
4. The Sprueing
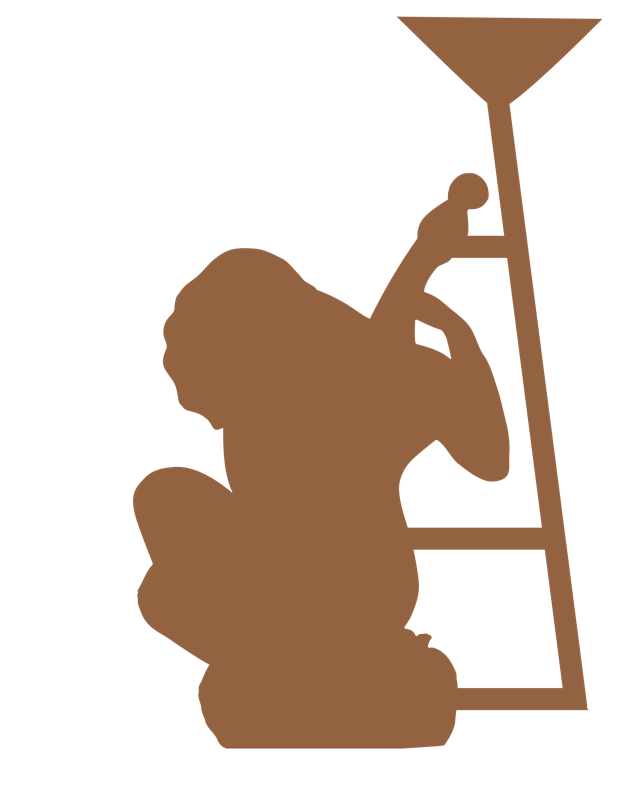
5. The Ceramic Shell Mold
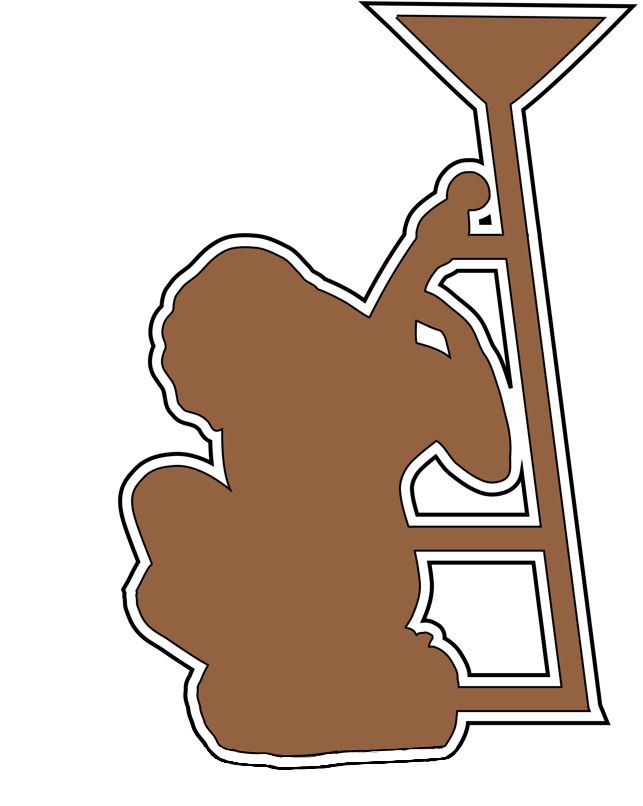
6. The Dewaxing
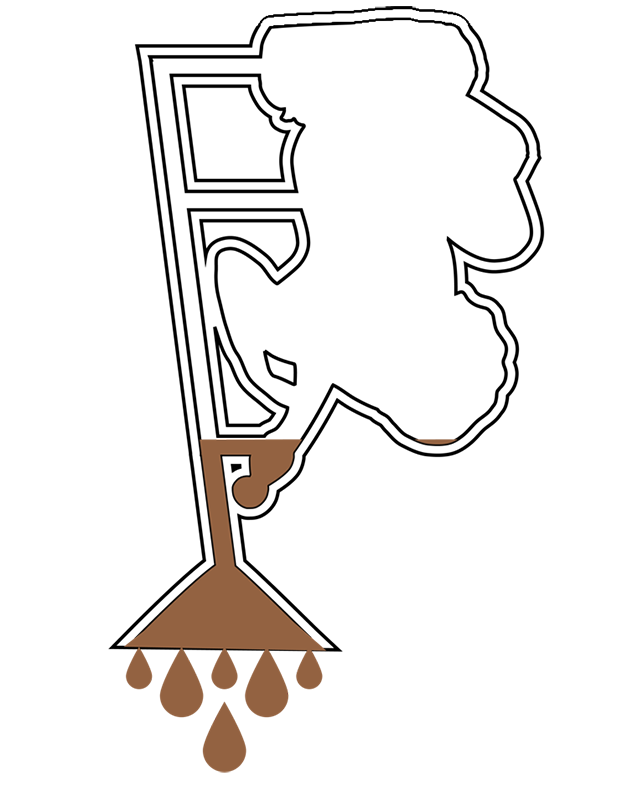
7. The Casting
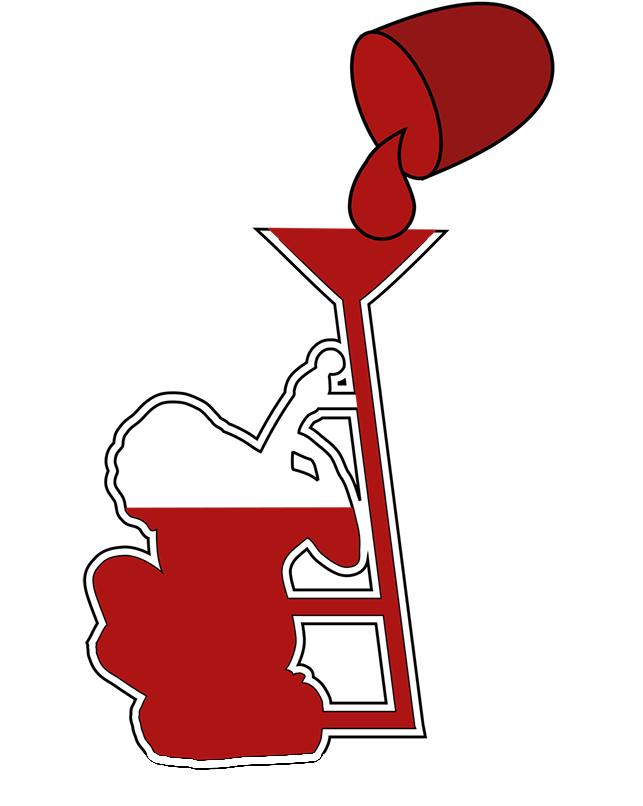
8. The Finishing
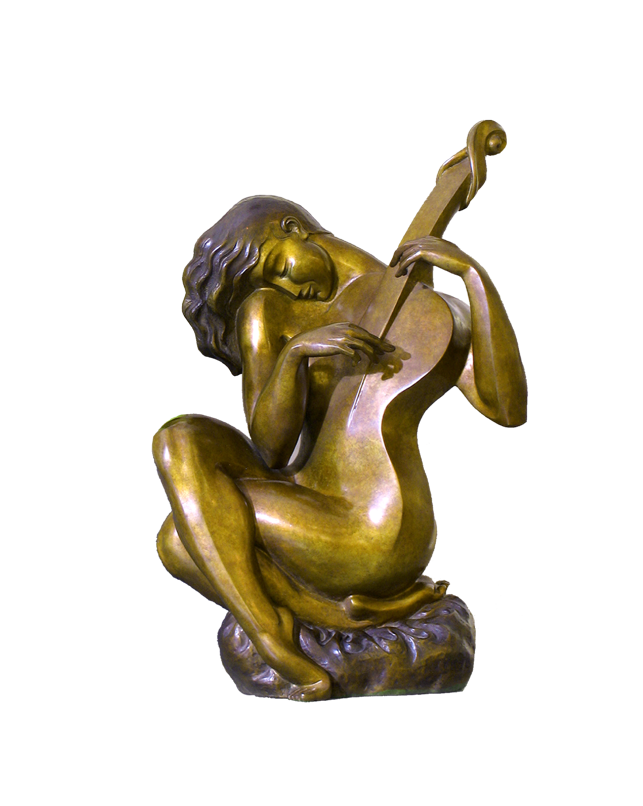
Care and Cleaning Instructions for Bronze Sculpture
Care for your artwork is simple, but it does require some knowledge and common sense.
Each bronze is covered with a “patina”, a coloration created at the foundry by applying different chemicals to the heated metal, which are then sealed with a wash of hot wax.
The patina “luster” is maintained by applying a very thin layer of hard wax (Trewax is the preferred brand) every three to six months, depending on how much of a polished finish you prefer.
Many awards have certain areas that have been highlighted in gold, the natural color of polished bronze. These areas should be polished only with a bronze cleaner, such as Simichrome. However, the bronze cleaner should be applied very carefully with Q-Tips, removed with a cotton cloth. It should never touch the patinaed areas or it will remove the coloration.
As with any artwork, do not place the sculpture outdoors or in direct light. The ultra-violet rays of the sun will cause discoloration in the sculpture. Over a long period of time the colors will eventually change due to the natural oxidation of metal.
If a change in coloration does occur, or if you would like to renew or change the patina color, you should contact a bronze foundry.
Follow these simple instructions and you will be able to enjoy the patina of your sculpture as much as you enjoy its gracious and dramatic form.
Care for your Clear Acrylic or Glass Award
Cleaning
Periodic light dusting with a damp, soft, clean cotton cloth is recommended. Optional: Once a year, wash your sculpture with a mild detergent and lukewarm water using a clean, soft cloth, or a sponge. Rinse well and blot dry with a soft, lint-free cloth. Never use abrasive cleaners, household cleaners, window cleaning fluids, or any products containing solvents such as alcohol or ammonia.
When cleaning products, such as those mentioned above, are in use in close proximity to the sculpture, the artwork should be covered with an enclosed cloth bag.
Polishing
Occasionally, use a mild acrylic cleaner found in most hardware stores or from plastic distributors to maintain the brilliant luster of the clear highly polished surfaces on the sculpture. (Product Recommended: Brillianize Acrylic cleaner.) Follow manufacturer’s instructions on the bottle. Polish only the clear surfaces of your sculpture.
Lighting
Note: Clear acrylic resin is heat sensitive. Exposure to heat in close proximity to your award sculpture may result in damage to the artwork. When displaying the sculpture on a lit pedestal, a light source with good ventilation is recommended.